Hydrogen production and storage capabilities
Thanks to our flexible, whole energy system approach, we are able to offer increased hydrogen production and storage capabilities across the Translational Energy Research Centre and the Sustainable Aviation Fuels Innovation Centre.
We are able to produce up to 150m³/h of green hydrogen, as well as additional blue hydrogen production capabilities. In total, we can store 1500Nm3 of hydrogen at 200 bar, which can be distributed across both sites.
Electrolyser for green hydrogen
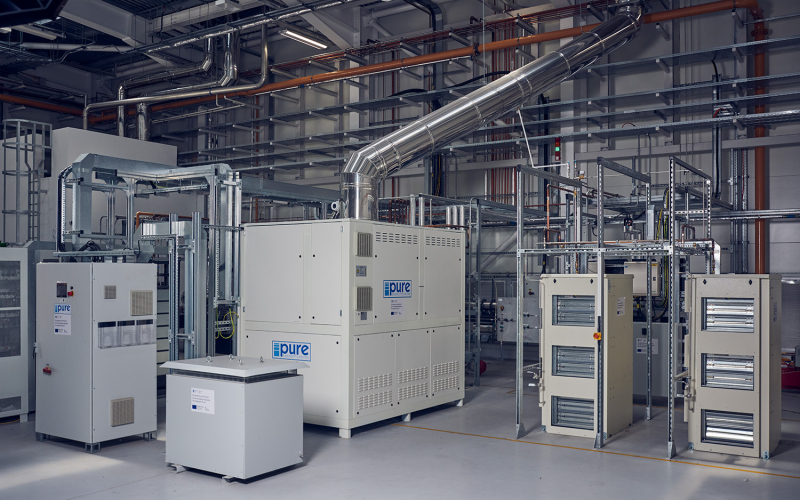
• A fully-automated hydrogen electrolyser which generates pressurised hydrogen, with a purity of 99.999%, from the electrolysis of water using an alkaline electrolyte
• Designed in a fail-safe mode with remote control and monitoring features
• Could produce up to 32 cubic meters of hydrogen per hour
• Equipped with a specialised compressor which brings up the pressure of the generated hydrogen to 200 bar
• The pressurised hydrogen is safely stored in a bank of cylinders with a storage capacity of more than 35 kg (>450 Nm³)
• Could operate with as low as -10°C ambient temperatures
IMI VIVO electrolyser for green hydrogen
As well as the above electrolyser, TERC also hosts an electrolyser from IMI VIVO which is capable of producing 110Nm3 per hour of green hydrogen with storage capacity of 1050 Nm3. This amount of hydrogen production capability, coupled with our other electrolyser, means the University of Sheffield is the university with the largest capacity for green hydrogen production in the UK, capable of producing the equivalent of the electricity required to power 200 homes.
• The IMI unit is a PEM electrolyser; the catalyst is a noble metal-based matrix with a proton conducting polymer (unlike our other electrolyser, which uses an alkaline liquor catalyst)
• Designed for fully automated, fail-safe operation with remote controland monitoring features
Hydrogen-powered gas turbine
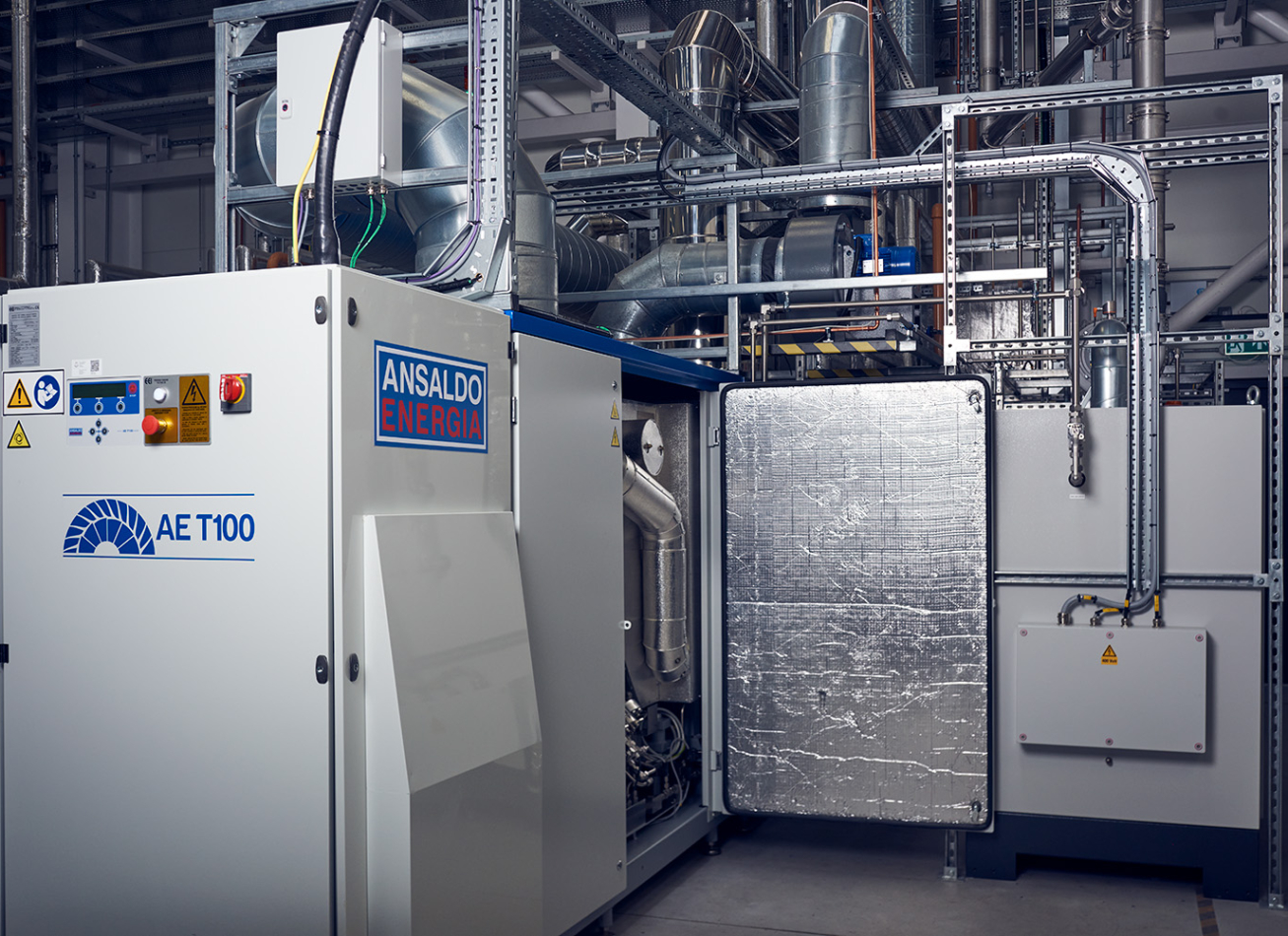
- The Turbec T100 micro gas turbine is highly instrumented to allow monitoring of the whole gas turbine cycle (temperatures, pressures, etc.), including extensive emissions analysis from the exhaust
- Conventionally fueled by natural gas, conversions are in place to fire a range of other fuels, including biogas
- Fuel flexibility research means that we are also investigating including hydrogen blending and other sustainable alternative fuels into our system
- The system comprises of a single-stage centrifugal compressor (with a pressure ratio of 4.5:1), a lean, pre-mixed combustion chamber and a single-stage radial turbine
- The generator and shaft rotate at up to 70,000 rpm to generate high-frequency electricity that is exported to the grid
- The counter-current water-gas heat exchanger is used to recover thermal energy; overall, the system has an electrical output of100 kW, with a thermal output of 165 kW (electrical efficiency ~30%; total efficiency ~80 %)
- The significant dilution ensures high combustion efficiencies and low levels of emissions (CO, NOx, etc.)
- The system has been modified to include exhaust gas recycle (EGR & Selective EGR), by which CO2 injections enable the examination of the impacts of recycling the exhaust gases on the combustion system, efficiency and emissions under different operating conditions
- Post-combustion CO2 capture research from the turbine system is available, since the flue gas pathway is integrated into the on-site capture systems
PEM fuel cell
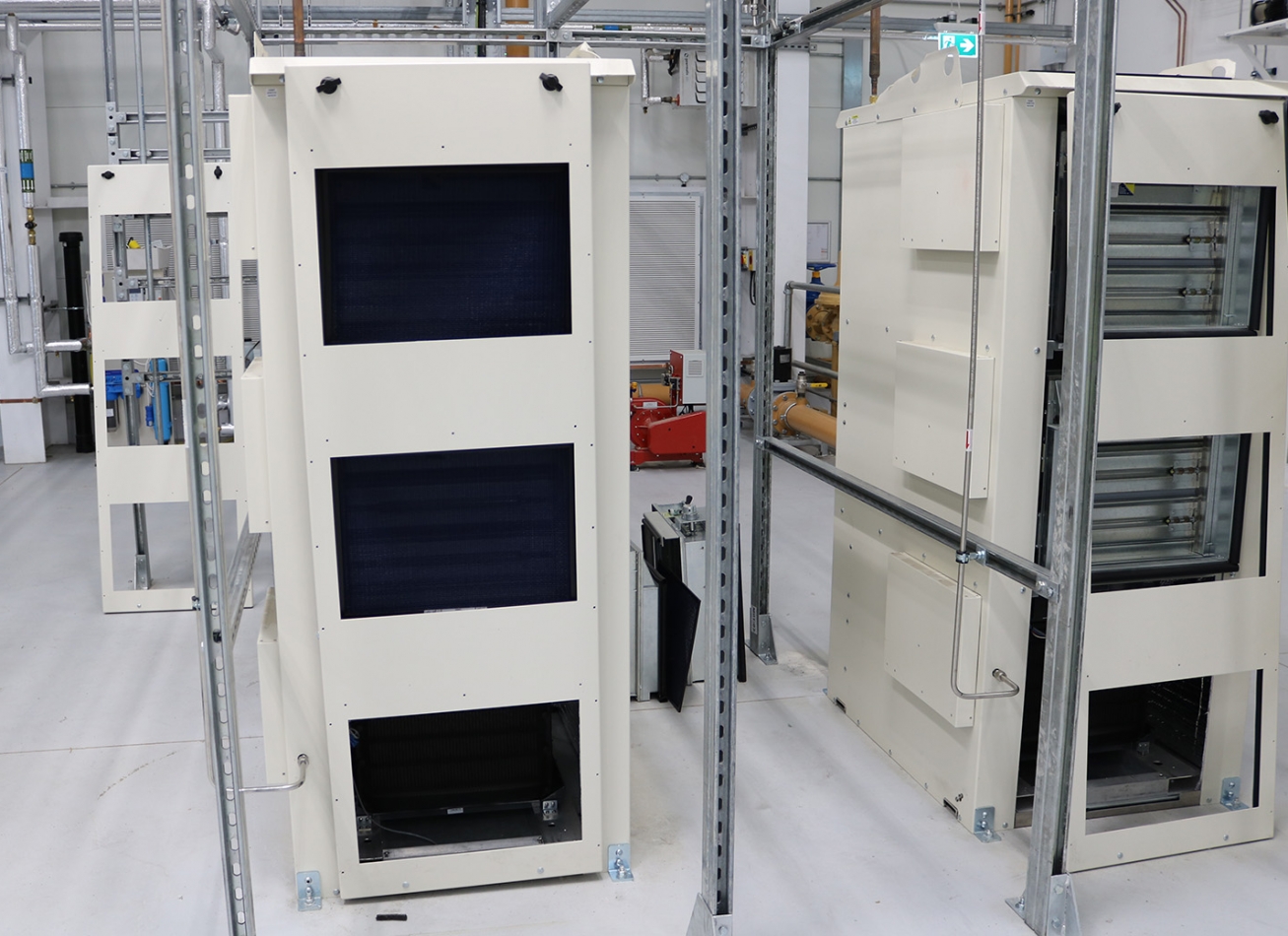
• Generates a power that could be used by the end user or sold to the national grid
• Provided with an internal bridge power system that enables instantaneous power generation from cold start
• Equipped with frost protection integrated utility that allows for operation at sub-freezing temperatures
• Operates at a wide range of pressures (2.7 to 10 bar) and relative humidity (5 to 100%)
• Has an integrated control and monitoring system
• Real-time monitoring of hydrogen consumption, electricity generation, fuel cell stack voltage and current, to name a few
Hydrogen Combustion Research Facility (HCRF)
- Undertake a wide range of analytical functions, including near burner analysis, heat transfer to load and furnace analysis, emissions analysis and burner design and performance analysis, as well as many other functions
- The HCRF is tailored for R&D activities. With 200-300kWth input and turndown to 50kWth and max. operating temp. of 1500°C; sized appropriately for industrial long flame burners (~3.5-4m)
- The HCRF supports fundamental and applied research on hydrogen combustion and cofiring with other fuels (primarily natural gas) in air as well as capability for oxy firing or oxygen enrichment; flame, heat transfer, and emissions characterisation; burner development; corrosion, deposition and materials research and other aspects of combustion research
Multi-parameter fuel cell test station
- The multi-parameter fuel cell test station will investigate the impact of the operating conditions (i.e. the temperature, pressure, gas composition and humidity) on single fuel cell or small fuel cell stacks
- It will be also used to investigate the effect of the new materials and/or designs on the fuel cell performance
- It will enable a multi-range electronic load with a maximum load power of 50 W. A current resolution ≤ 10 mA. A mass flow controller for anode: ≥ 2 SLPM. A mass flow controller for cathode: ≥ 2 SLPM. Temperature-controlled humidifiers for the reactant gases. A fuel cell software for computer-controlled cell operation and experimentation. measurement for the real-time cell resistance